The double impeller pump is one of the most common mechanical power sources in various industries. They are estimated to contribute approximately 10% of the world's energy consumption. Pumps are usually used to move liquids, like water, oil, and gas, and are used in different kinds of systems. In this paper, the authors propose a new concept to rearrange impeller vanes in double suction centrifugal pumps to increase their efficiency. This innovation has potential to reduce GHG emissions.
The novel impeller design consists of a set of vanes, which are cross-vaned. A number of benefits were found from this innovative vane arrangement, including reduced blade loading, better flow guidance at the impeller outlet, and more effective axial and radial velocities. It also avoids instabilities.
The performance of the novel impeller has been evaluated in numerical and experimental modes. These results show that the new configuration can improve the global efficiency of the pump and can be retrofitted to existing impellers. Additionally, it can also reduce the slip factor of the pump and reduce its environmental impact.
Using the newly proposed configuration, the authors also investigated the effect of a staggered angle on the pressure distribution. As the staggered angle is increased, the pressure distribution becomes more uniform. Similarly, a small perturbation between the two pressure zones also affects the pressure distribution in the volute. This small disturbance induces a mixture of the fluids from the different impellers. However, the pressure fluctuations are offset by the superposition of the two impellers.
In addition to the novel impeller, the authors have also developed a new design process. By combining a 1-D computational model with a CFD simulation, the authors have developed a new approach to designing pumps. While previous designs were made through finite element analysis, this new process takes the guesswork out of the equation by applying a computational model directly to the pump's construction.
Using the RNG k-e model, the authors were able to accurately predict the rotating flow in the flow passage components. To investigate the effects of the novel impeller, the authors simulated the inner flow of the pump and investigated the velocity and pressure fields at the impeller outlet. Among other things, the authors found that the diameter of the hydraulic blades had a significant impact on the performance of the pump.
Another thing to note is that the novel impeller has a lower head coefficient than the conventional back-to-back configuration. This is to minimize stall. The motor parameters are then optimized to maximize the efficiency of the pump. For this purpose, soft packing material is used to avoid leakage along the shaft.
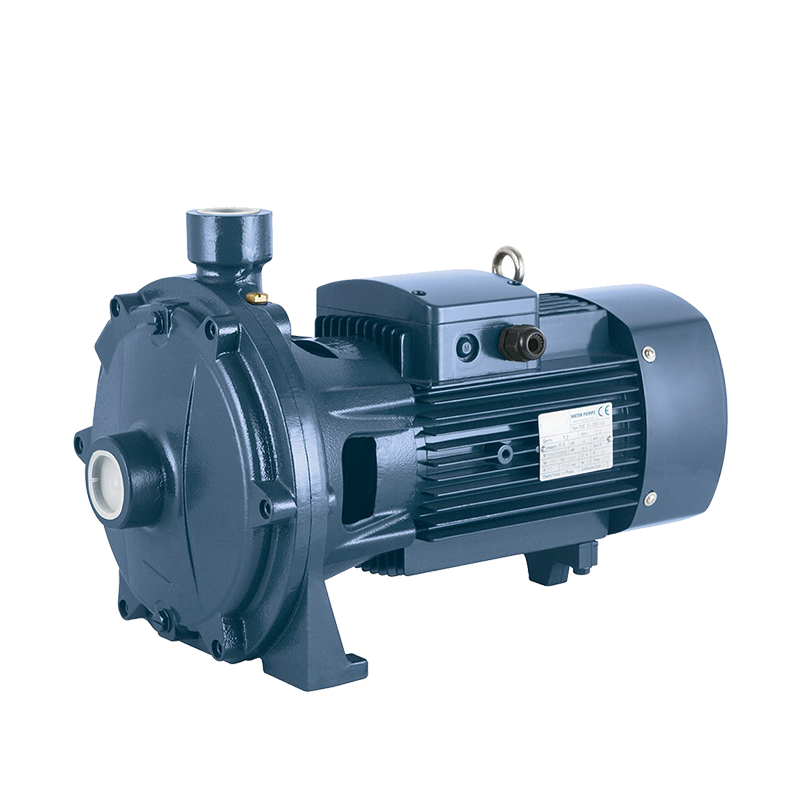
- DN Range of Suction Pipe: 32-50 mm (2"-4")
- DN Range of Discharing Pipe: 32-50 mm (2"-4")
- Flow Capacity Range: 0-120 GPM
- Head/Pressure Range: 2-16 Bar
- Power Range:1.1-22kw